No more cracked floors
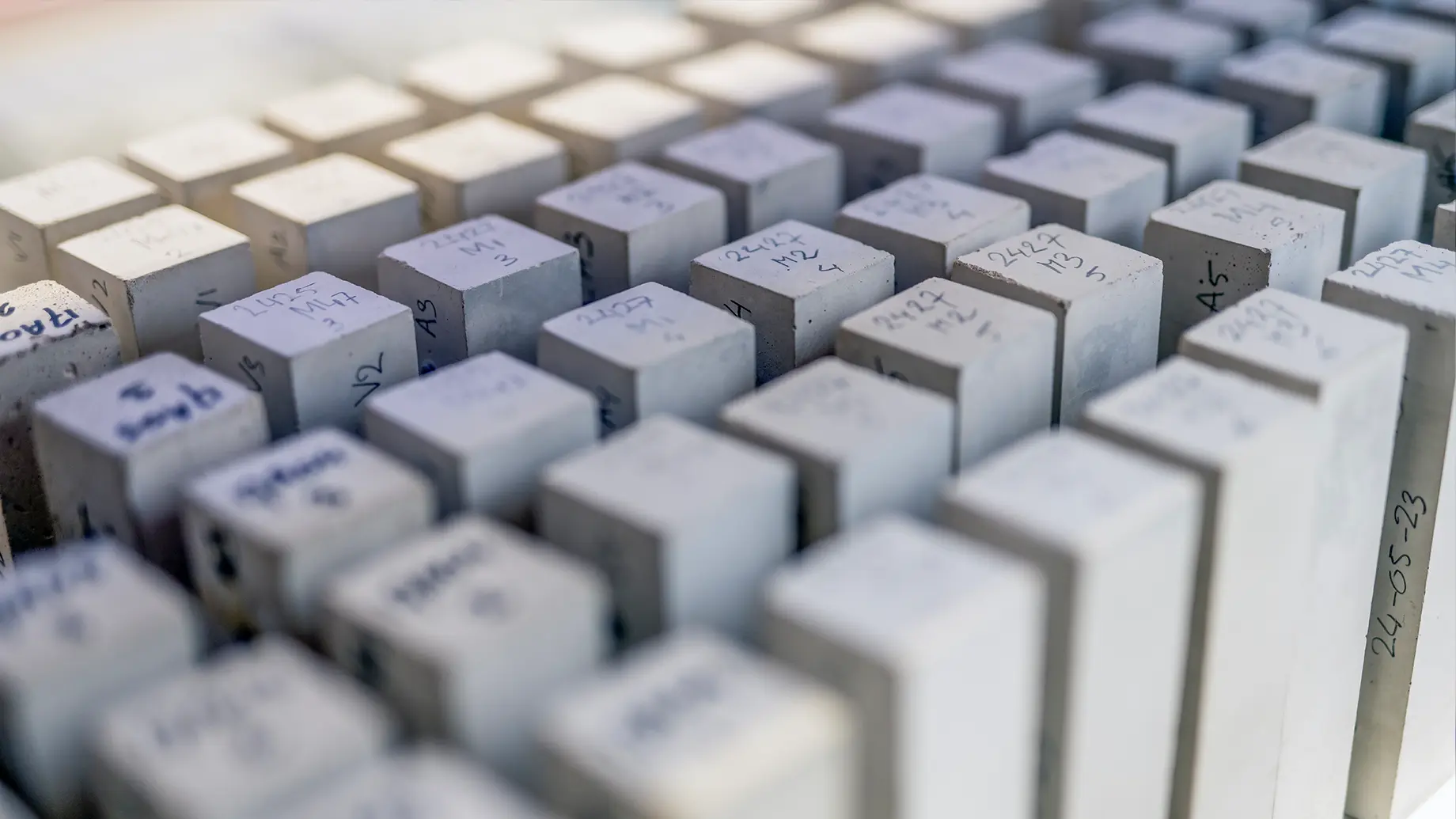
No more cracked floors
Concrete mix designed on the cutting edge of technology
Concrete isn’t affected by shrinkage cracks and requires much less CO₂ with the optimal spacing between the sand grains and gravel aggregates. It comes down to precise measuring, fitting, and some secret ingredients. Van Berlo came up with a revolutionary method to achieve this. The concrete mixers that arrive on site carrying the innovative mixture can’t go straight to the concrete pump. Their first stop is the mobile laboratory for quality control, where Van Berlo’s concrete specialists meticulously dose various admixtures to give the mixture the right properties. A bit of mixing in the mixer’s drum and the concrete mortar is ready for pouring. “It takes some extra work, but gives you superflat floors without any cracks”, says Nick Vervoort, head of R&D at Van Berlo. “We can also achieve up to a 50 per cent reduction in CO₂ emissions by using less cement and rebar. That ticks all the boxes for the large industrial floors for which we developed this innovation.”
Laserdiffraction
When it comes to sustainability, there is still a world to be won in the concrete mortar industry and Van Berlo did not want to lie around for others to do it for them. So, in 2017, the specialist in logistics concrete floors teamed up with TU Eindhoven on a five-year research project to do away with a chronic problem in concrete: crack formation. After the research project ended, the company took the next step by setting up its own R&D department with concrete technologists and a concrete laboratory. This resulted in a cutting-edge technology that has already been applied in several major reference projects.
The secret behind Van Berlo’s innovation is the sophisticated analysis method that uses laser diffraction. This high-tech analysis employs static light scattering to reveal the concrete composition down to powder level. It allows you to measure down to the tiniest detail which aggregate diameters a particular powder consists of. By including these findings in a so-called aggregate packing model, you can develop a concrete recipe that fills the voids between the sand and gravel aggregates with precisely the right powders, resulting in a dense structure that requires considerably less cement to glue the aggregates together. Above all, the mixture hardly shrinks when it is curing. That’s important because this is precisely what causes cracks.
Especially in large, jointless industrial floors, you need a lot of extra reinforcement to manage shrinkage cracks. Low water content and the use of special admixtures further reduce shrinkage behaviour. The exact composition remains our secret weapon. Using aggregate packing models isn’t new to concrete plants. But they definitely don’t go as far as Van Berlo. “Most concrete plants stop measuring aggregate diameters when they reach the size of sand grains. We go down to the powder particles”, says Vervoort. “That’s why we don’t need much cement to fill all those microcavities.” In standard industrial floor mixes, about 350 kilos of cement goes in per cubic metre. Van Berlo needs just 260 kilos. So a quarter less. Only a small percentage of that is Portland cement, the rest is blast furnace slag. Because there’s no shrinkage, you need less reinforcement. The floor is also roughly a centimetre thinner, which adds up to a substantial CO₂ reduction.
Mixture
The amount of cement could be reduced even further if regulations weren’t a restricting factor. 260 kilos per cubic metre is in fact the prescribed minimum for indoor flooring. If you go below that, you have to go through a separate testing procedure for every new floor. It’s also – still – a problem when working with geopolymer concrete.
Doesn’t the low water content in the optimised concrete mix affect the processing capability? This was true in the initial tests, but further development made the mixture less sticky. Still, applying it in practice on building sites remains challenging. The Van Berlo mixture doesn’t have the usual buffers for absorbing temperature fluctuations and moisture ingress, for example from rain pouring down on sand and gravel storage. “Conventional concrete mixtures can withstand that, but ours is designed to be on the cutting edge”, says Vervoort. “That’s why we inspect it on site. The information is then used to customise the ‘base concrete’ that was designed in the concrete plant.”
The floor does become slightly more expensive per square metre, depending on the cracking and CO₂ reduction required. This is due to using admixtures and the extra operations that are involved. Van Berlo is therefore working on automating the process. The ideal machine will be able to perform sensor measurements and independently add the required admixtures. “This does come at a cost”, admits Vervoort. “Our logistics floors are ‘Champions League-level’ floors in terms of concrete. This innovation means that expensive crack repairs are a thing of the past. In the end it’s not just the price that matters, but the yield per square metre.”