Keine Rissbildung
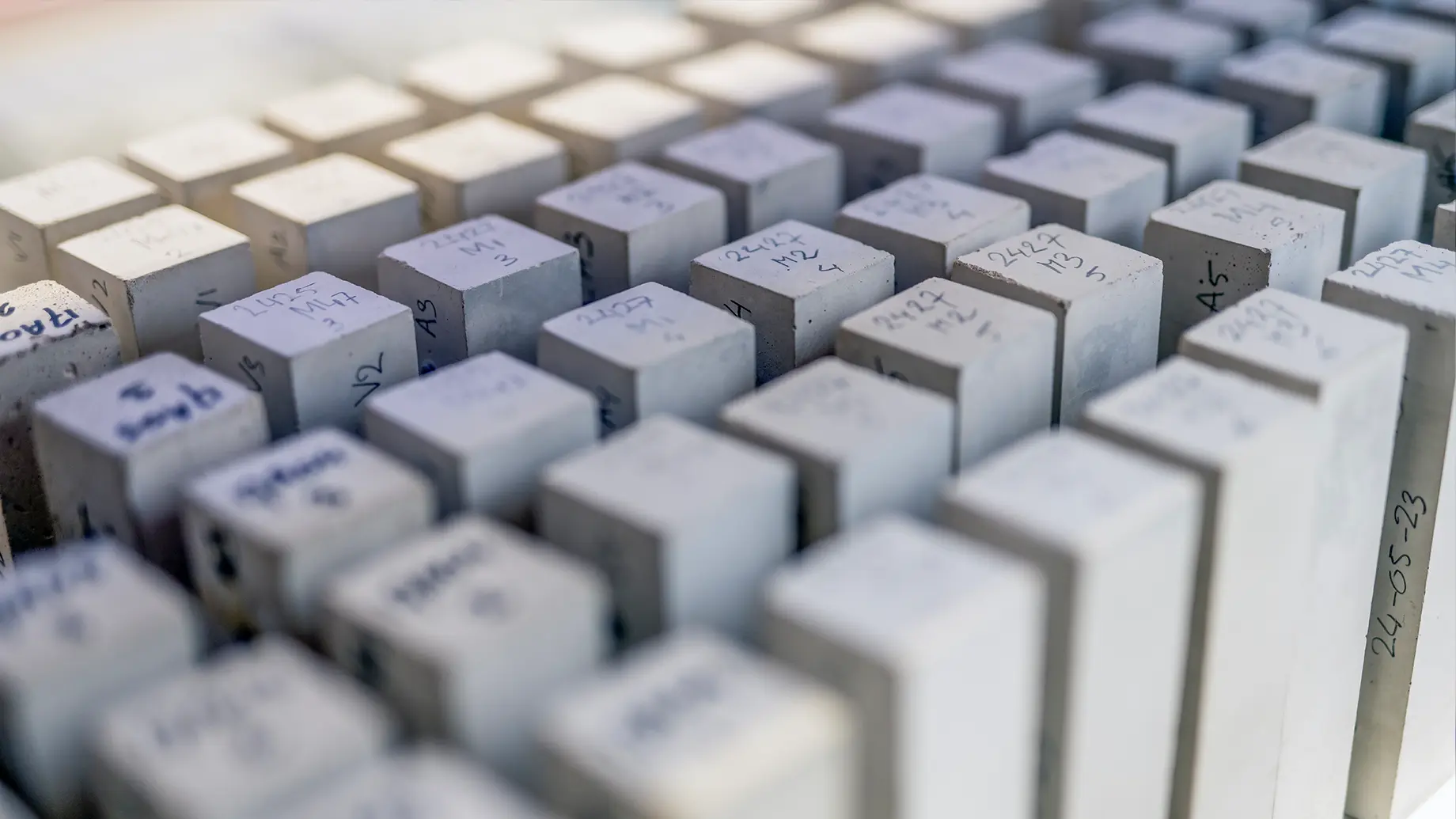
Keine Rissbildung
Rissbildung in Böden ein Ende gesetzt, Betonmischung mit engsten Margen entworfen
Der Beton weist keine Kriechrisse auf und hat bei optimaler Nutzung der Räume zwischen Sand- und Kieskörnern einen viel geringeren CO₂-Ausstoß. Eine Frage des präzisen Einfügens und geheimer Zutaten. Van Berlo hat sich hierfür eine revolutionäre Methode einfallen lassen. Die Betonmischer, die mit der innovativen Mischung gefüllt auf der Baustelle ankommen, können nicht gleich zur Betonpumpe gefahren werden. Sie müssen zuerst zur Qualitätskontrolle in das mobile Labor. Dort dosieren die Betonspezialisten von Van Berlo verschiedene Hilfsstoffe, um der Mischung die richtigen Eigenschaften zu verleihen. Kurz durch den Betonmischer und der Mörtel ist gebrauchsfertig. „Das macht etwas mehr Arbeit, aber das Ergebnis sind superebene Böden ohne Risse“, erklärt Nick Vervoort, Leiter F&E bei Van Berlo. „Außerdem reduzieren wir unseren CO₂-Ausstoß durch die Verwendung von weniger Zement und Bewehrung um bis zu 50 Prozent. Das macht sich bei den großen Industrieböden, für die wir diese Innovation entwickelt haben, ganz schön bemerkbar.“
Laserbeugung
In der Betonmörtelindustrie besteht, was Nachhaltigkeit angeht, noch sehr viel Raum für Verbesserung, doch Van Berlo wollte nicht auf die Innovationen anderer warten. Also schloss der Spezialist für Logistikböden im Jahr 2017 mit der TU Eindhoven einen Kooperationsvertrag für eine fünfjähriges Forschungsprogramm zu Beton, das dem chronischen Problem der Rissbildung ein Ende setzen sollte. Nach Abschluss diese Programms setzte das Unternehmen die Forschungsarbeiten in einer eigens dafür eingerichteten F&E-Abteilung mit Betontechnologen und Betonlabor fort. Das Ergebnis war eine weiterentwickelte Technologie, die in mehreren großen Referenzprojekten zum Einsatz kam.
Das Geheimnis hinter der Innovation ist eine äußerst verfeinerte Analysemethode. Van Berlo nutzt dazu die Technik des Laserbeugens. Diese Hightech-Technik macht die Zusammensetzung des Betons durch statische Lichtstreuung bis auf Pulverebene sichtbar. Hiermit lässt sich genaustens messen, welchen Korndurchmesser ein bestimmtes Pulver besitzt. Diese Erkenntnisse fließen in einem so genannten Kornpackungsmodell ein, wodurch es möglich ist, ein Betonrezept zu entwerfen, in dem die Zwischenräume zwischen den Sand- und Kieskörnern mit den entsprechenden Pulvern gefüllt werden. Dies führt zu einer dichten Struktur und einem bedeutend geringeren Bedarf an Zement, um die Körner miteinander zu verleimen. Zudem zieht sich die Mischung beim Aushärten kaum zusammen. Das ist wichtig, denn genau das verursacht die Risse.
Vor allem in großen, fugenlosen Industrieböden wird eine zusätzliche Bewehrung benötigt, um Kriechrissen entgegenzuwirken. Durch einen geringen Wassergehalt und die Zugabe spezieller Hilfsstoffe nimmt das Kriechverhalten noch weiter ab. Die genaue Zusammenstellung dieser Stoffe ist ein Betriebsgeheimnis. Die Verwendung von Kornpackungsmodellen ist für Betonwerke kein Neuland. Doch sie gehen dabei nicht annähernd so weit wie Van Berlo. „Das Betonwerk hört bei der Bestimmung des Korndurchmesser auf der Ebene eines Sandkorns auf, wir gehen bis zu den Pulverpartikeln“, erklärt Vervoort. „Deshalb benötigen wir weniger Zement, um diese Mikrolöcher zu füllen.“ Bei einer normalen Mischung für Industrieböden werden rund 350 Kilo Zement pro Kubikmeter verwendet, bei Van Berlo-Beton sind das nur 260 Kilo. Also ein Viertel weniger. Nur ein kleiner Anteil davon ist Portlandzement, der Rest ist Hochofenschlacke. Da der Beton nicht kriecht, kommt auch weniger Bewehrung zum Einsatz. Der Boden ist am Ende etwa einen Zentimeter dünner. Das macht sich bei der CO₂-Bilanz deutlich bemerkbar.
Mischung
Die Zementmenge könnte sogar noch weiter reduziert werden, wenn die gesetzlichen Vorschriften dem nicht entgegenstünden. 260 Kilo pro Kubikmeter ist für Innenböden nämlich das vorgeschriebene Minimum. Begibt man sich darunter, muss für jeden Boden eine gesonderte Testreihe durchlaufen werden. Dieses Problem stellt sich uns auch bei Geopolymerbeton – zumindest noch.
Wirkt der geringe Wassergehalt in der optimierten Betonmischung sich nicht auf die Verarbeitbarkeit aus? Bei den ersten Tests war dies noch der Fall, doch durch die Weiterentwicklung wurde die Mischung weniger klebrig. Trotzdem bleibt die Verwendung in der Praxis auf der Baustelle eine Herausforderung. Die Van Berlo-Mischung hat nicht die üblichen Puffer, um Temperaturschwankungen und die Einwirkung von Feuchtigkeit auszugleichen – zum Beispiel durch einen Regenschauer über dem Sand- und Kieslager. „Konventionelle Betonmischungen können das verkraften, doch unsere Mischung wurde mit engsten Margen entworfen“, so Vervoort. „Deshalb führen wir auf der Baustelle Kontrollen durch, auf deren Grundlage dem von uns entworfene „Basisbeton“ aus dem Betonwerk noch Hilfsstoffe nach Maß zugesetzt werden.“
Dies macht den Boden je nach gewünschter Riss- und CO₂-Reduzierung pro Quadratmeter etwas kostspieliger. Das kommt durch die verwendeten Hilfsstoffe und die zusätzlichen Arbeitsschritte. Aus diesem Grund arbeitet Van Berlo an der Automatisierung des Prozesses. Die Wunschmaschine führt Sensormessungen durch und mischt die benötigten Hilfsstoffe selbständig hinzu. „All das ist mit Kosten verbunden“, so Vervoort. „Unsere Logistikböden sind im Betonbereich wahres „Champions League-Niveau“. Dank dieser Innovation gehören teure Rissausbesserungen der Vergangenheit an. Letztendlich kommt es jedoch nicht nur auf den Preis an, sondern auch auf den Ertrag pro Quadratmeter.“