Business intelligence gives grey matter colour
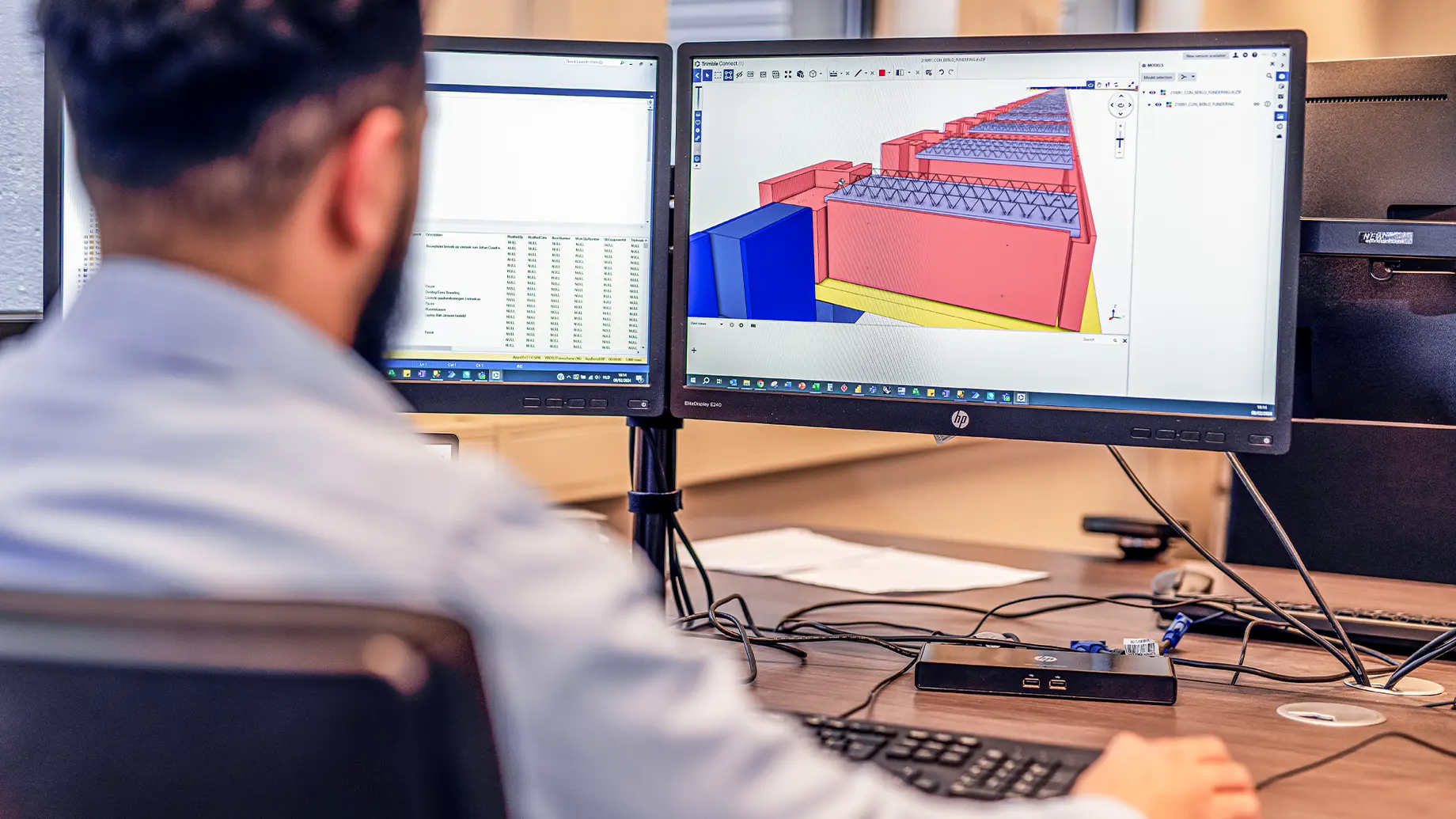
Business intelligence gives grey matter colour
With a relatively large surface area compared to the volume, industrial floors are one of the most difficult and error-prone niches in the concrete market. Whereas concrete mortars generally have a forgiving bandwidth, concrete floors tend to show virtually every blemish as soon as you look at the surface. What’s more, the almost daily changing properties of the natural raw materials make designing, producing and processing the ideal mixture -even with identical project specifications- by no means a one-off feat.
Concrete flooring: certainly no easy feat
Never content with our market-leading position in this complex niche, both in quality and volume, we have set ourselves the resolute goal -on top of the above challenges- to be a pioneer in durable, sustainable and crack-free floors. This innovative technology -the result of years of R&D in our laboratory and co-development with TU Eindhoven- overcomes a multitude of technological challenges and apparent contradictions, but therefore requires an unprecedented narrow bandwidth for the variable properties of the concrete mortar and processing. This allows us to continually meet our market-transcending quality standards.
If we see even the smallest chance, we insert sensors This complexity and narrow bandwidth mean that our high-end, sustainable and crack-free concrete is no longer attainable using the conventional production methods of concrete plants. All things considered, it is a massive challenge in terms of concrete technology and processing. So how is it that we have successfully poured more than 75,000m² of industrial floors, while others find it very hard to achieve comparable quality, even without sustainable and crack-free properties?
Business intelligence: our secret weapon
To stay ahead in this complex playing field, we focus on real-time process control: from collecting and testing the initial raw materials through to delivery of the ready-to-use floor. Our aim in the process is to measure and manage the entire production chain. To this end, we have developed three processes that use supporting hardware and software: VB Sense, VB Data Factory and VB Insights. Powerful algorithms are constantly at work to identify, classify and connect all data points in real time
VB Sense
VB Sense enables us to measure, monitor and record every single process step through an extensive network of apps and a variety of sensors connected to proprietary developed portable VB Sense Hub minicomputers that collect data 24 hours a day and 7 days a week. So what do we actually measure? The list of what we don’t measure would be a lot shorter…if it can be measured, we stick sensors in it. Before any project gets underway, we measure raw material lab tests, optimum aggregate packing, mortar compositions, compression, flexural tensile and shrinkage tests, concrete recipes, substrate measurements and measurements at the concrete plant(s), and we calculate the influences of weather forecasts. On the day of pouring, we monitor the supply, mortar composition and mortar properties before and after pumping, the pumping speed and pumping pressure, the finishing and post-treatment, and we record everything in real time on video for follow-up analysis. After pouring the floor, we do extensive measurements of strength development, wear resistance, flatness, skid resistance and the crack pattern. Furthermore, we perform long-term lab tests and keep our sensors embedded in the floor and other sensors on the floor attached, so we can continue to generate valuable data for years(!) to come. You might even say that VB Sense is all our technological feelers rolled into one.
VB data factory
The VB Data Factory is complex software we have developed our secure cloud that wirelessly receives and processes all data, 24 hours a day and from all over the world. The software uses powerful algorithms to identify, classify and connect all data points in real time, and archive the data in our Business Intelligence databases. This is where all data points from (partial) processes, research/results and cause/effects connect to one another: from the very first aggregate tests to the very last step of post-treatment. This actually does justice to the name: a factory where individual data points are assembled into powerful insights.
VB Insights
Insights is where all information comes together in software with powerful tools to gather new insights -a kind of detective in concrete technology- with artificial intelligence and big data trend analyses as its assistants. As the dataset grows over time, VB Insights use AI to gradually gather more capabilities to generate automatic alerts, advice and even preventive warnings. But VB Insights is not only of value to our R&D experts. Other disciplines such as engineering, project support, executive teams, but also sales and even our management, benefit directly from the many insights into quality assurance, innovation and cost reduction. Valuable insights that help us stand even more firmly and serve our customers even better.
One more thing…
There is just one last seemingly insurmountable obstacle…. the fact that concrete plants aren’t able to produce our concrete mix within our unusually narrow bandwidths using their conventional production processes. Does this mean a sad and early demise of our pioneering technology? Of course not! To us, there is only one solution: taking control of the very last step of concrete mortar production. Without giving away too much about our patent-pending developments, we can divulge that we are in the final development stages of a truly fantastic machine that transforms concrete mortar from virtually any low-grade form to high-end Van Berlo concrete in real time. And how do we plan to produce our innovative new concrete until that miracle machine is finished, you wonder? By simply doing what Van Berlo has always done: good old hard work and perseverance. The steps that will soon be performed fully automatically are now being done by hand. Whether that’s hard work? At TEAM Van Berlo, we smile and say it’s ‘just another day on the job’.
We saw only one solution: taking control of the very last step: concrete production.