Circular and low-carbon concrete floor
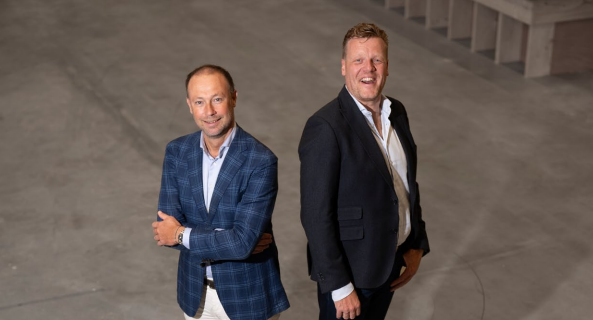
Circular and low-carbon concrete floor
Circular and low-carbon concrete floor:
Breakthrough for New Horizon and Van Berlo
Logistics flooring and industrial halls are needed in our economy, but their carbon footprint and depletion of primary raw materials are not. How can we build without doing harm to the environment? New Horizon and Van Berlo have joined forces to answer that question with revolutionary steps in circularity and innovative technology to reduce CO2 emissions. Erik Koremans, Director of Material Balance at New Horizon, and Frans van den Biezenbos, Commercial Director at Van Berlo, are incredibly proud of their joint breakthrough: a crack-free concrete floor that is fully circular. “We’re actually writing history.”
Don’t demolish but harvest New Horizon was founded eight years ago with the slogan: ‘We don’t demolish, we harvest’. Its ambition: to get a circular construction economy off the ground and scale it up. “We use the city and not the earth as a resource”, explains Erik Koremans. “We do this by harvesting the purest possible waste flows when buildings are torn down and, together with partners in the Urban Mining Collective, reusing those resources in new development projects. This substantially reduces CO2 emissions and lets us close environmental circles.” The Material Balance division of New Horizon,is responsible for (re)supplying the market with a wide range of circular building materials and raw materials obtained from urban mining.
One of those building materials is concrete. “We a grateful that we can partner with Rutte, a large sustainable concrete producer, so that together we can recover the original components – sand, gravel and cement – from harvested blocks of concrete and reuse them in the production of new circular concrete. Rutte uses Smart Liberator technology to reclaim sand, gravel and cement. Compared to traditional concrete aggregates – broken pieces of old concrete – this technology achieves an unparalleled quality improvement in circular concrete.”
New Horizon looks beyond just concrete and collaborates with producers of other building materials. Koremans: “We’re working with Wienerberger, for example, to turn old bricks into new ones. Distribution partners such as Stiho and Rexel then make sure that contractors and installers can buy the circular building materials. We have found solutions to complete the circles for various raw materials that are extracted through urban mining.” Sustainable and crack-free Van Berlo takes the lead in improving the quality and sustainability of large concrete industrial flooring. Frans van den Biezenbos: “We didn’t wait for innovations from the concrete mortar industry. To this day, there are still no innovations available (i.e. scalable, affordable and within the applicable regulations) that can make our concrete floors more sustainable, improve them or replace them.”
In 2017, Van Berlo teamed up with the Technical University of Eindhoven on a five-year research study to analyse crack-free concrete for large industrial floors. Afterwards, Van Berlo continued on its own to develop this technology further. The result is a revolutionary solution that makes floors sustainable – up to 50% less CO2 emissions – and crack-free. The secret? A unique concrete mix, a new way of building, and 24/7 monitoring. For each project, the raw materials available for the concrete mix are thoroughly analysed in the Van Berlo laboratory. Using the high-tech method of laser diffraction, Van Berlo’s concrete engineers design and test the sustainable and crack-free concrete mixes. Van Berlo uses up to 25% less cement and water in the concrete to achieve its goals. This reduces the concrete’s carbon emissions by about 35% and ensures the concrete remains free of cracking. Van den Biezenbos: “Thanks to the quality improvement of crack-free concrete, we can now even achieve CO2 savings of up to 50%. That’s because you don’t need as much steel rebar or concrete in crack-free concrete.” The technology to achieve sustainable and crack-free floors starts with an innovative concrete mix, but ultimately consists of a total package of measures. These include on-site checks, sensor-based monitoring, high-quality execution and post-treatment of the floor. “Our engineers are always happy to tell you more about our innovation”, says Frans van den Biezenbos.
Why this combination? Concrete industrial floors in large distribution centres are extremely important for efficiency and reliability when handling logistics processes. “Concrete shrinkage is a natural phenomenon that causes cracking in floors of these large sizes, which can hamper the logistics processes. Moreover, floors like this represent up to 50% of the building’s total carbon pollution”, says van den Biezenbos. By combining circular raw materials from New Horizon with Van Berlo’s low-CO2 and crack-free concrete technology, the customer can count on a sustainable quality solution. “Together, we have the opportunity to drastically reduce the CO2 impact of a building”, says Koremans. “So I just want to say this: join us!
We have a fantastic solution and we can take on the market. But we can only supply circular concrete floors if we also have enough donor buildings to harvest. That way, we can unite to make an even greater impact and work towards a real system change.” And finally, this floor helps you prepare your business for the future. “See it as a pre-investment”, says Koremans. “Legislation is getting tougher and carbon pricing is surely coming. Production and building methods that pollute are starting to cost a lot more. With that rising demand, low-carbon flooring will become a scarce product in the near future. Companies that choose us already today will get the exclusive right to delivery after the carbon pricing.” Seeing is believing, “But don’t just take our word for it”, says van den Biezenbos. “Drop by any time for a cup of coffee and we’ll happily take you on a visit to reference projects so that everyone can see the spectacular results with their own eyes.”